Description
MUTOH 1625mm wide Dye-Sublimation Printer
Dual head CMYK roll-to-roll
MUTOH’ s new XpertJet 1642WR Pro is a 64” – 1625mm wide water-based inkjet printer with a new platform that inherits the properties of the XpertJet series. Two new extra-wide print heads achieve high productivity with incredible print speed and the highest print quality thanks to best-in-class dot placement accuracy. Various new features provide improved user convenience.
The XPJ-1642WR Pro delivers high-quality graphics for a wide range of applications such as trade show graphics, flags, banners, custom interior designs, apparel, sports uniforms, and more, and brings the best “Made in Japan Quality” to the various markets.
DOWNLOAD BROCHURE:
MUTOH XPJ-1641SR-P Brochure
Outstanding benefits

High-Speed Production
Print speed of over 15m² per hour.

Automation
MUTOH’s latest unique automated technologies provide user efficiency and consistent high-quality prints.

Incredible Print Quality
The new ‘AccuFine’ print head achieves outstanding print quality even at high speeds.

Head Height Adjustment
Four-level adjustment of 1.5mm, 2.0mm, 2.5mm, and 4mm to allow for optimal printing clearance.

Highest Quality Print

The ‘AccuFine’ print head is wider and delivers higher density with more accuracy than conventional print heads achieving both high-speed printing and excellent image quality. Even at high speed, the ‘AccuFine’ print head can produce high-quality solid printing with less banding.

Conventional head

Increased nozzle row length contributes to higher productivity

Conventional head

High density nozzle pitch contributes to higher image quality
High Productivity with ‘AccuFine’
Throughput of XpertJet 1642WR Pro (m2/h)

NEW Print Effect ‘i-screen’

The new print effect ‘i-screen’ created from MUTOH’s ‘Intelligent Interweave’ printing technology, optimizes the new print head ‘AccuFine’. By arranging the dots in a way that takes into account how they look, reducing banding for smoother print images.
Conventional effect

i-screen

MUTOH’s Unique Technologies for Automation and Efficiency

An automatic bi-directional alignment system has been added to the existing ‘DropMaster technology’, and it has evolved into DropMaster 2. The built-in sensor on the carriage automatically calibrates bi-directional alignments, saving time and reducing variation in adjustment among operators.
Before Drop Master 2


Without automatic bi-direction
After Drop Master 2


With automatic bi-direction

By printing a print pattern and reading it with a sensor, paper feed correction can be automated. This reduces the time and effort required for adjustment and media loss.

Before automatic feed correction
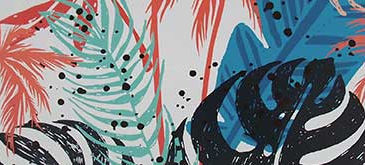
After automatic feed correction

By printing a barcode on the end of media, the printer will read the barcode and recognize the amount of media remaining when the media roll is loaded at a later date.
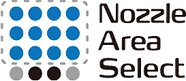
In the event of blocked nozzles, printing can be performed temporarily using only active nozzle blocks, maintaining print production and print quality.
Automatic Nozzle Checking Unit
The automatic nozzle checking unit can optically monitor firing nozzles from the print head, missing nozzles can be detected automatically and nozzle cleaning can be performed reducing operators’ workload.
If nozzles are not recovered, the Nozzle Area Select function automatically activates to continue printing.
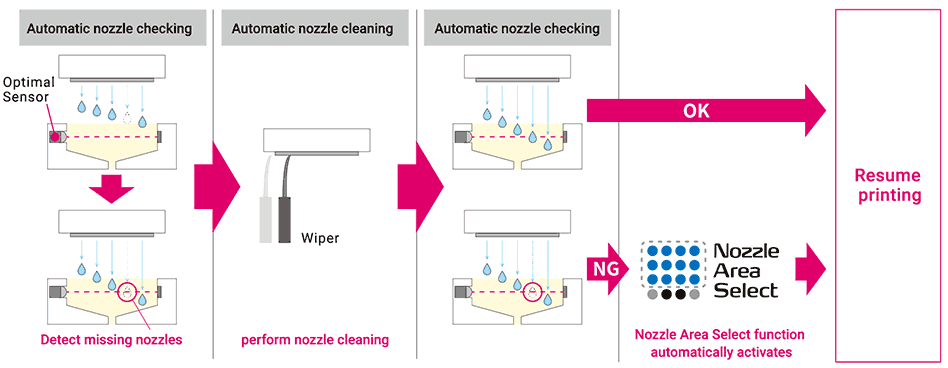
High Media Compatibility
Head Height Setting
Select the optimal print head height 4 available options depending on the media being used. This reduces the risk of contact and also maintains the highest print quality.
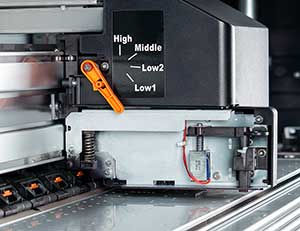
High: 4.0mm
Middle: 2.5mm
Low 2: 2.0mm
Low 1: 1.5mm
Pressure Roller Control
Media feeding power is affected by pressure and paper thickness. This pressure mode can be set to four levels: high, middle, low, and partial pressure by adjusting the position of the media set lever and the pressure arms, which expands media feed capability.
Thin paper and soft media that could not be fed by conventional sublimation machines can now be supported by setting the pressure low. Media cockling can now be minimized by individually disengaging multiple pressure rollers.
A wide range of media types can be fed under optimal conditions and combined with the optional heavy-duty take-up system expand media handling capability.

Media Set Lever

Pressure Arm

Optional Heavy Duty Take-Up
Built-in Heater and Exhaust Fans

The XPJ-1642WR Pro features a built-in heater improving ink drying allowing for continual high-speed printing.

Sublimation transfer printing often uses a higher head gap that can cause issues for heavy uses such as ink mist inside the printer, ink dripping from the exhaust fan, etc.
Additional exhaust fans have been added on both sides of the printer to minimise this.